π A Truly Smart Factory is a Safe Factory
Hello engineers! Hermes Solution brings you this week’s comprehensive guide on implementing functional safety based on the IEC 61508 standard. As smart factories buzz with advanced robotic arms and conveyor belts, productivity has improved remarkably. However, haven’t you ever wondered: “As automation equipment increases, doesn’t the risk of safety accidents also grow?”
The transition to smart factories has accelerated dramatically, leading to unprecedented improvements in productivity. However, increasingly complex automation systems are creating new forms of safety risks. In modern manufacturing environments where robotic arms work tirelessly and autonomous guided vehicles navigate factory floors, the question “Are all these automated systems operating safely?” has become more critical than ever.
IEC 61508 is an international standard for functional safety of electrical/electronic/programmable electronic (E/E/PE) systems. Rather than simply adding safety devices, it presents a systematic safety management approach throughout the entire safety lifecycle. This guide will comprehensively cover the core concepts of IEC 61508 and practical implementation methods.
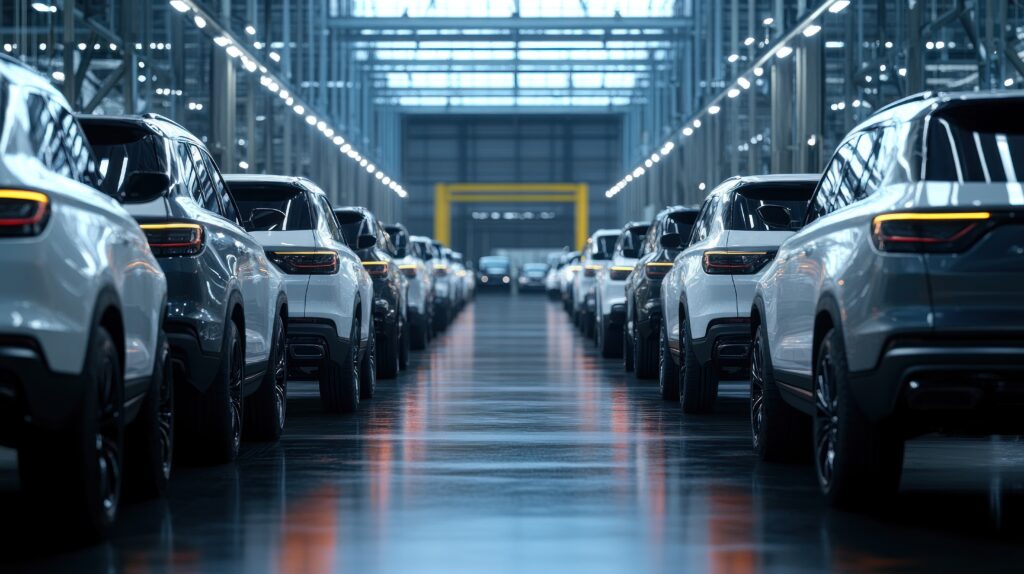
π What is Functional Safety?
Functional Safety refers to the ability of a control system to detect hazardous situations and transition to or maintain a safe state. IEC 61508 defines this as “the part of the overall safety of the EUC (Equipment Under Control) and EUC control system that depends on E/E/PE safety-related systems.”
π Why is Functional Safety Important?
Traditional manufacturing facilities primarily relied on physical protection devices (safety fences, protective covers, etc.). However, smart factory environments introduce new risk factors:
Software Defects: Errors in complex control logic or unexpected situations
System Interactions: Previously safe independent systems becoming hazardous when integrated
Cybersecurity Threats: External intrusions compromising safety systems
Sensor and Communication Failures: Malfunctions due to incorrect information
These risks are invisible but can cause catastrophic consequences, making systematic functional safety approaches essential.
π‘οΈ IEC 61508-Based Functional Safety Implementation Strategy
IEC 61508 defines functional safety not as an element added at the end of development, but as an essential component that must be systematically managed throughout the Overall Safety Lifecycle. This integrated approach considers and manages safety at every stage from system concept to decommissioning.
π What is Functional Safety?
Functional Safety refers to the ability of a control system to detect hazardous situations and transition to or maintain a safe state. IEC 61508 defines this as “the part of the overall safety of the EUC (Equipment Under Control) and EUC control system that depends on E/E/PE safety-related systems.”
π Why is Functional Safety Important?
Traditional manufacturing facilities primarily relied on physical protection devices (safety fences, protective covers, etc.). However, smart factory environments introduce new risk factors:
Software Defects: Errors in complex control logic or unexpected situations
System Interactions: Previously safe independent systems becoming hazardous when integrated
Cybersecurity Threats: External intrusions compromising safety systems
Sensor and Communication Failures: Malfunctions due to incorrect information
These risks are invisible but can cause catastrophic consequences, making systematic functional safety approaches essential.
π‘οΈ IEC 61508-Based Functional Safety Implementation Strategy
IEC 61508 defines functional safety not as an element added at the end of development, but as an essential component that must be systematically managed throughout the Overall Safety Lifecycle. This integrated approach considers and manages safety at every stage from system concept to decommissioning.γ
Expert Personnel Acquisition
Successful IEC 61508 standard implementation requires Functional Safety Engineers (FSE) as key personnel. They must possess not only technical requirements knowledge but also practical application experience, with certified consultant support when necessary.
Cost Optimization Strategy
Risk-based approaches should allocate appropriate SIL to each hazard. Excessive safety levels generate unnecessary costs, making it important to derive the most economical solutions within acceptable risk levels.
Industry-Specific Standard Application
IEC 61508 provides a comprehensive framework standard. Machinery should apply sector-specific standards like ISO 13849 or IEC 62061, while process industries should use IEC 61511 to clarify practical implementation.
Systematic Documentation Management
All activities and decisions throughout the entire safety lifecycle must be documented for traceability. This is essential for certification acquisition, regular audit responses, impact analysis during system changes, and responsibility determination in case of accidents.
βοΈ Machinery Safety Standards Framework
IEC 62061 – Safety of Machinery: Safety-related electrical, electronic and programmable electronic control systems
Sector standard derived from IEC 61508 for machinery
Uses Safety Integrity Level (SIL) concept
Provides requirements specific to electrical/electronic control systems
ISO 13849 – Safety of Machinery: Safety-related parts of control systems
Covers all technologies (electrical, hydraulic, pneumatic, mechanical)
Uses Performance Level (PL) concept
Combines category structure with probabilistic approach
π Standard Selection Guide
Electrical/Electronic Control-Centered Systems
IEC 62061 application suitable
Complex programmable logic performs major safety functions
SIL-based quantitative reliability calculation feasible
Multi-Technology Systems
ISO 13849 application recommended
Hydraulic, pneumatic, mechanical elements involved in safety functions
Integrated evaluation of diverse technologies possible
Highly Complex Systems
Consider direct IEC 61508 application
Complexity difficult to handle with machinery standards
New technologies or specialized applications
π‘ Practical Implementation Considerations
Standards can be used complementarily, with the most suitable standard as the main framework while referencing other standards’ concepts as needed. The key is consistently applying the chosen standard and meeting all its requirements.
β Conclusion: Functional Safety as Investment for Smart Factory Sustainability
IEC 61508-based machinery functional safety implementation goes beyond regulatory compliance to become essential investment for smart factory sustainable growth. While pursuing production efficiency and innovation, it represents the most fundamental commitment to protecting worker lives and corporate assets.
Key Success Factors:
Technical Excellence:
Systematic hazard analysis and SIL determination
Objective decision-making through quantitative risk assessment
Independent, reliable safety system design following IEC 61508 principles
Robust architecture ensuring safety even during failures
Lifecycle Management:
Comprehensive functional safety management from development to operation
Continuous safety performance maintenance and improvement
Organizational Infrastructure:
Expert personnel acquisition, cost efficiency, related standard integration, thorough documentation
Essential infrastructure for successful implementation
These elements have become core competencies that all smart factories and industrial automation companies must possess. Through the compass of functional safety, we can build safe and productive future smart factories.
A factory without accidents is truly a smart factory. Join Hermes Solution in creating a smart and safe future through IEC 61508-based functional safety!